Shanghai Pan Zhihua Machinery Manufacturing Co.,LTD is located on the third largest island of China municipal industrial park----No.898,San Sha Hong Road. Among the company’s 160 staffs them,25 people have high-level technical title.The total area of the factory is 38000 square meters,with standard workshop 19800 square meters.
-
Normal Speed Non-continuous Pilger Mill
Advantages: Low maintenance cost Easy operation Low break-down rate (servo structure) Product with high precision Characteristics: 1)The transmission of the main transmission system is carried out by either mean:1) Using a high-strength nylon-based flat transmission belt, in which the str
94 -
Normal Speed Continuous Pilger Mill
Advantages: Low maintenance cost Easy operation(One person can operate two devices) improved yield (improved by 20% to 30%) Low breakdown rate (servo structure) Product with high precision Characteristics : 1)The continuous feeding and rolling device is increased, and therefore the yield
145
- Contacter: Mr Fan
- Tel: 86-21-15201793197
- Fax:
- Email: pzh@shpzh.com.cn
-
Company Address:
No.898,San Shahong Road,Chongming Industrial Park,Shanghai city,China
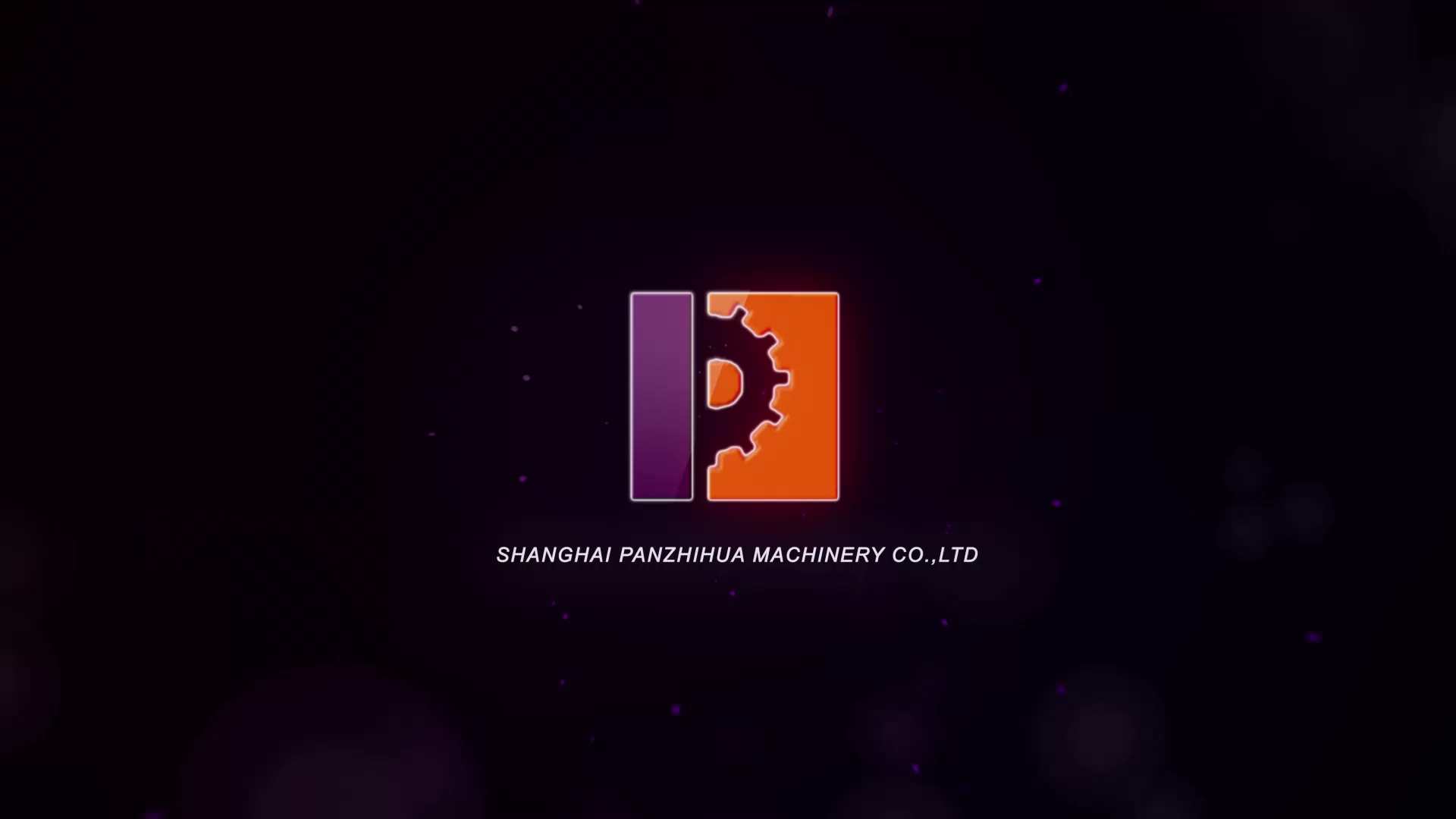
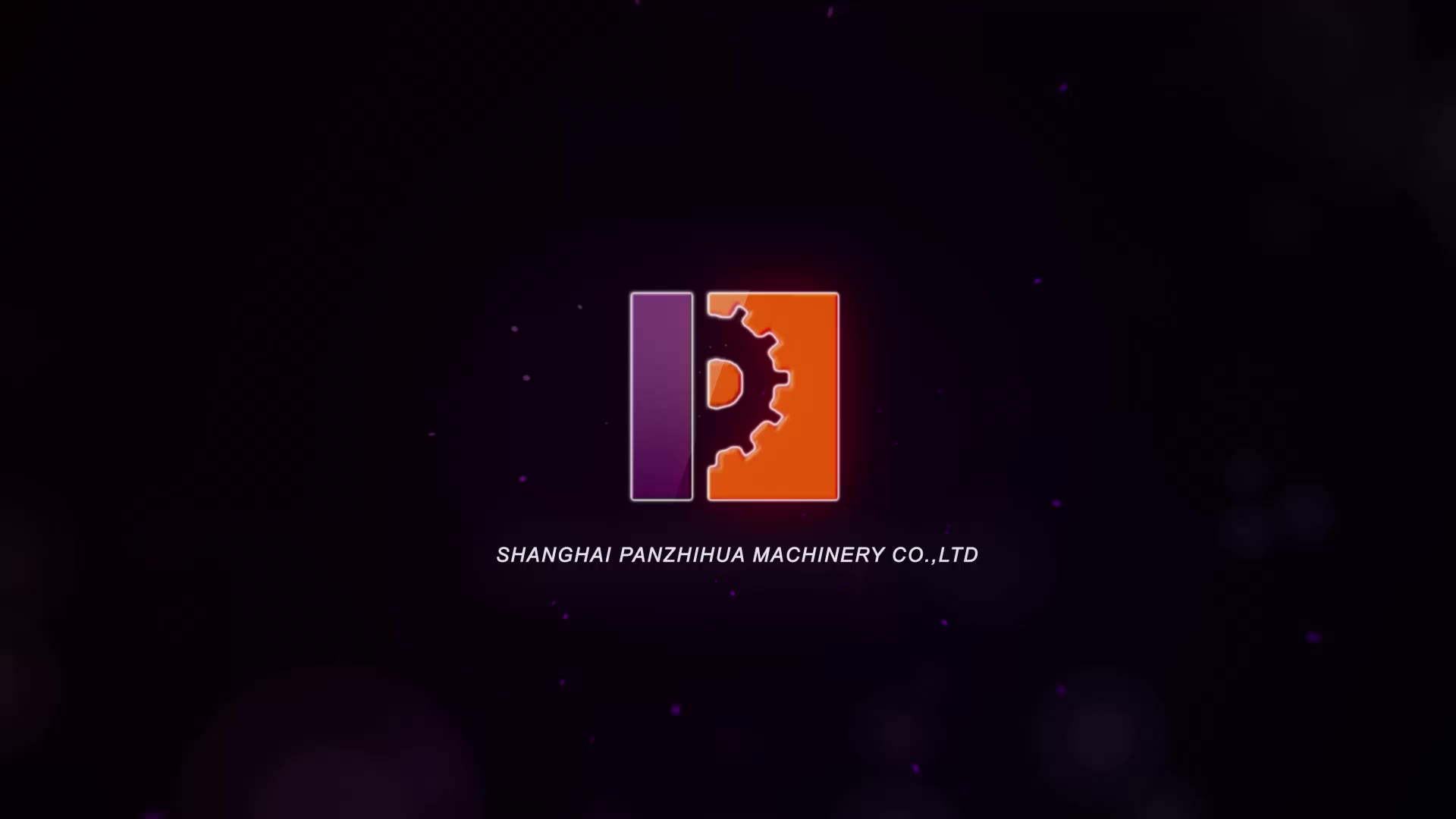
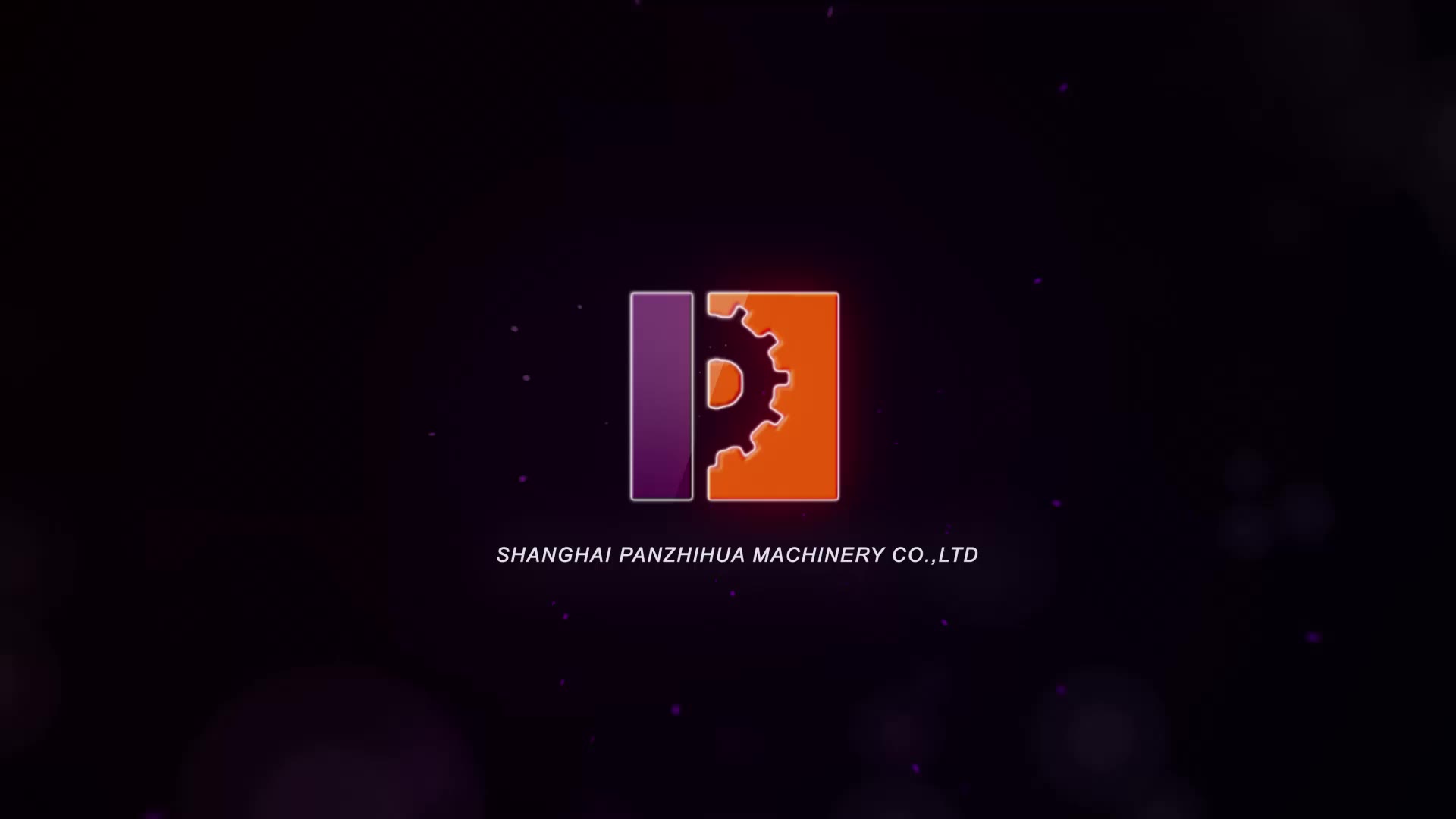